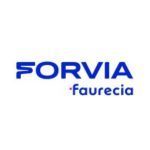
FORVIA
Job Description
Overall Responsibilities And Duties:
The role of a Program Quality Leader (PQL), as a part of the program core team, is to represent the customer voice within Faurecia and ensure compliance with all quality deliverables.
The main missions of the role are:
Focus on the customer specific requirements, assess program specific risks, investigate similar product, and process performance and prepare QTS (Quality Target Study) deliverables for validation
Sets the initial Program Quality objectives (Safety& Regulation, 0 Km, Warranty, perceived quality, and specific customer quality indicators), cascade them to the internal and external supplier, based on the key deliverables and ensure the realization.
Ensure that program quality KPIs are available for all relevant parties, prepare and escalate identified risks appropriately within Daily Core Team meeting (SLI, 8D, …), PRC, …
Ensure the respect of Quality targets defined and launch necessary actions if not at target and drive results.
Monitor the objectives achievement through a risk assessment follow up based on FMEA, Special characteristics, capabilities, Tolerance stacks, PPM, etc
Assess the relevant risks and trigger alert to the appropriate management level, if necessary
Is responsible for conformity, perceived quality and traceability of any parts delivered to the customer all along the development phase until Gate 4.
Ensure the use of the appropriate methods and quality standards (PMS, specific customer program development system, international regulations, 10 Quality Basics in Engineering and Development, Process Qualification Audit, D&P-FMEA with focus on early risk assessment, Quality Target Study, KPC& KCC list, Control Plans for all phases, PIST & PIPC, Convergence Plan, etc…)
If applicable, implement Meisterbock process and ensure quality objective achievement.
Verify& approve the “Design Validation Plan” and “Production Validation Test” established by Engineering and ensures its completion according to the program milestone
Checks the specification for measurements, checking and testing fixtures and gauges and ensure the integration into the calibration system.
Define and update with the support of relevant function (PML, PDL, IPL, etc…) the definition of the control plan for prototype, pre-series, and series phases.
Responsible for the PPAP approval of intercompany parts
Prepare and approve the PPAP files and the submission of the initial samples, including process validation audit.
Actively contributes to continuous improvement process within program, capitalize and transversal lessons learned then feedback information to product & process standardization committee , manage complexity and customer focus.
Support the program manager in the daily program problem solving (SLI / 8D) activities
Support the program manager to achieve the customer satisfaction objective: demerit, convergence plan, etc…
Support the program manager to prepare gate reviews, dashboard, PLR and functional milestones as related to the quality function
Initiate and update the Program Risk Assessment. Alert if major risk has no contingency plan (AMS, etc…)
Be the Customer Quality Contact and satisfy related information demands (Customer APQP tracking, Audit Support, 8D communication until SOP)
Lead functionally all Program related Quality resources (Prototype Quality, Advanced Supplier Quality, New Program Quality…) to assure a consistent and aligned Quality Objective deployment & progress tracking process
Ensure on time delivery of PQL related PMS work packages and key deliverables of Program Phases
Has the authority to stop any process or product delivery in case of serious non-conformance (customer expectations or safety and regulations issues…)
Qualifications
The ideal candidate will have/be:
Minimum education level: Quality or Production Engineer Bachelor with equivalent combination of education and experience
Experience:
Minimum 8 ~10 years of quality or engineering experience in Automotive industry specific to Welding process, (Exhaust commodity would be prefarable)
Customer relationship experience on Royal Enfield or any 2 Wheeler commodity would be preferable.
Skills and competencies:
Solid knowledge of Quality in Program and Production
Strong understanding of Functional analysis, FMEA, Control Plan and statistics analysis.
Strong analytical and proven team problem solving skills.
Ability to anticipate issues and provide solutions to complex problems.
Continuous improvement attitude
Ability to develop quality mindset within teams in his/her perimeter.
Team player with strong communication and interpersonal skills.
Good in verbal and written communication skills. Good level of English.
Team player with strong attention to detail and remains calm under pressure.
Nice to have working knowledge of ISO standards, Customer specific requirements.
To be strong on APQP process.