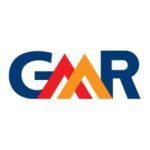
GMR Group
JOB PURPOSE
To Ensure the Unit/Station availability as per AOP plan ,stick to 100% statutory compliance adopting safe and trouble free technology ensuring the value addition to all stake holders converting maint wing into a profit centre from cost centre
ORGANISATION CHART
Accountabilities
Key Performance Indicators
Ensuring plant availability
Plan and ensure adherence to PM schedules
Plan and execute capital overhauls and planned shutdowns without time and cost overrun
Ensure quality repairs avoiding premature failures /repeat jobs
Liaison with statutory authorities for timely renewals
Availability of station as per AOP
Planned overhauls without no time overrun
100%statutory compliance
Resource management
Selection of quality vendors for maintenance activities
Selection of competitive vendors based on quality for supply of spares and consumables
Plan the spares considering the lead time so that maint schedules stick to time frame decided
Mobilization of resources catering to critical path adoption
Indigenization of foreign spares for reduction in lead time and cost
Indegenization of vendors at least for 80% of spares and services
Skill evaluation of service providers and skill enhancement programme as needed
Planning,Budget control and asset management
Assessment of plant condition using monitoring techniques
Evaluation of lifecycle study depending on control measures
Management of asset life cycle
Inventory control by proper scheduling of consumption
Idenifications and implementation of modification and upgradations for efficiency and reliability improvement
Budget planning depending on production sched mplementation of mo edule and shutdown activities
No overrun from budgeted values
Demarkation in items budgeted with clear value breakups
No of modifications implemented
Inventory reduction
Non moving items life reduction
No over run in budget
No emergency sanction of extra budget
No surplus budget at the year end
Cost control measures adoption
Chaning the nomenclature of cost centre to profit centre
Adopting best practices in the sector for bench marked maint practices
Indegeniztion of spares
Alternate vendor development for cost effectiveness
Quality consciousness adoption in repairs
Avoiding time overrun in planned repairs by effective resource mobilization
Avoiding over maintenance and repetitive maintenance
On job skill enhancement of team for effective resource utilization
Maint cost within budget
No cost overrun in the planned repairs
No emergency procurement
Reduction in lubricating oil consumption by 5%
Reduction in maint cost b y 8% over previous year
KEY ACCOUNTABILITIES
Accountabilities
Key Performance Indicators
Establishment of Quality Plan
Imbibing quality consciousness in all maint activities
Every repair as planned in schedule SMP
Developing SWI and SMP for all activities
Establishing and adopting WPS
Training the team to have certified quality inspectors
IMS , OHSAS implementation
Bench marked repair standards with specified values
No NC in IMS implementation
SWI and SMP modified versions
Bench-marking safety standards:
On job training at regular intervals
Ensuring incident investigation to avoid major occurrences
No unsafe incidents
Lifting tools and tackles compliance
No of safety trgs organized
On job training and EHS awareness
Value addition to stake holders
Making work place environment friendly with impeccable house keeping
Adopting 5S techniques
Establishing bench marked practices
Eco friendly power generation at optimal cost
Specific fuel consumption and auxiliary power consumption as per AOP
Reliability of station as per agreed terms
Zero discharge adoption
Emissions well within norms
Planation as per agreed norms
APC best in the industry
Team Development.
To build a team capable of running the established system
Infuse confidence and capability into the team
Making the things system driven than man driven
Data interpretation and analysis
On job training
Competency building by job specific trainings
EXTERNAL INTERACTIONS
Interaction with all vendors for timely ,cost effective and quality based job execution
Liaison and technical interaction with statutory authorities
State government authorities & Central government authorities to obtain statutory clearance/Permission
Scientific and investigative agencies and educational institutions for case studies
INTERNAL INTERACTIONS
Interaction with customer mainly operations for their complaint redressal and ensuring reliable equipment availability
Interaction with other department heads for timely completion of jobs
Interaction with team members for their capability enhancement and grievance redressal and knowledge sharing.
Quality wing for establishing bench marked standards
FINANCIAL DIMENSIONS
Maintenance budget with in AOP target
Reduction in consumable cost by 5%
Capital overhauls with in 18 days
Indigenization of spares for cost reduction by at least 7 crore per annum
OTHER DIMENSIONS
EDUCATION QUALIFICATIONS
Bachelor Degree in Mechanical Engineering
RELEVANT EXPERIENCE
Behavioral Competency
Personal Effectiveness.
Networking & External Orientation.
Teamwork & interpersonal influence.
Execution & Result.
Planning & Decision Making.
Problem solving & Analytical thinking.
Technical Competencies
Activity Management.
Spare Cost Management.
SME
HIRA, JSA, SAI Management.
Resource Management
COMPETENCIES
Personal Effectiveness
Social Awareness
Entrepreneurship
Problem Solving & Analytical Thinking
Planning & Decision Making
Capability Building
Strategic Orientation
Stakeholder Focus
Networking
Execution & Results
Teamwork & Interpersonal influence