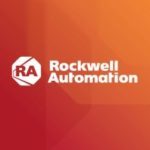
Rockwell Automation
Rockwell Automation is a global technology leader focused on helping the world’s manufacturers be more productive, sustainable, and agile. With more than 28,000 employees who make the world better every day, we know we have something special. Behind our customers – amazing companies that help feed the world, provide life-saving medicine on a global scale, and focus on clean water and green mobility – our people are energized problem solvers that take pride in how the work we do changes the world for the better.
We welcome all makers, forward thinkers, and problem solvers who are looking for a place to do their best work. And if that’s you we would love to have you join us!
Job Description
Job Summary
Provide clear leadership for the development of an environment focused on Quality. Develop quality-process links with customers in line with the Quality Management system, Production Part Approval Process (PPAP), Controls Plans, Failure Mode and Effect Analysis (FMEA) and Supplier Quality Assurance (SQA) processes and oversee continued compliance and embedding across the business. Responsible for maintaining relationships with internal customers and suppliers to maximise profit potential and ensure efficiency. Manage the audit program and work proactively with all Managers, Supervisors and Employees, to maintain a program of continual improvement within their areas of responsibility. Lead a ‘correct at source’ and problem-solving methodology (Lean). Lead the team to achieve quality targets for customers and business goals.
Key Responsibilities
• Contribute to the creation and implementation of best practice quality vision, strategy, policies, processes and procedures to aid and improve operational performance
• Contribute to new business initiatives and projects and review and communicate the impact on Quality activities General and Task Management
• Ensure that all in-house systems and procedures are updated, revised and modified to meet the needs of external certification bodies
• Respond to customer complaints putting in containment actions, full analysis, poka-yokes (error proofing), and implementing short-term and long-term countermeasures
• Champion a program for the implementation and sustainment of a continuous improvement culture
• Ensure that all necessary systems and procedures are in place to satisfy all customer requirements and audits
• Introduce new systems and procedures where appropriate
• Train others in all aspects of the quality system and application of procedures
• Undertake internal and process audits of the Quality Management System (QMS)
• Management of the Quality Engineers and Technicians in the sign-off of parts and the resolution of internal/external quality concerns
• Establish and refine quality sign-off instructions, standards and documentation
• Report against agreed quality metrics on a monthly basis
• Lead regular inspection meetings with representatives from appropriate departments to establish an action plan for improving build quality
• In conjunction with the Supplier Quality Assurance function, reduce the effect of non-conforming supplier materials on the production area quality
• Perform root cause analysis and resolve problems
• Identify business improvement opportunities within the organization
• Develop, implement and manage key performance indicators (KPIs) for each area of responsibility
• Set department objectives/KPIs and review and assess ongoing performance of direct reports
• Ensure KPIs are met by working to the overall plan, including management of, and reporting
• Report on achievement of targets and identify any actions required
• Manage, coach and develop a high performing Quality Operations team that meets agreed objectives, and which delivers best practice results, added value and continuous improvements
• Manage and lead the team, ensuring adequate staffing levels
• Consistently promote high standards through personal example and roll out through the team so that each member of the team understands the standards and behaviors expected of them
• Review, implement and update company records e.g. training matrices, performance reviews, risk assessments
• Work collaboratively, negotiate and engage with key stakeholders to facilitate delivery and compliance with the Quality strategy
EDUCATIONAL QUALIFICATIONS / WORK EXPERIENCE
(Education, qualifications and experience requirements an employee must have)
• Bachelor’s Degree in engineering
• Minimum 15 years’ experience with >5 years in management capacity.
• High product mix, high demand variability, significant product line depth, mix of standard and configured products.
• Candidates must have a high energy level, the demonstrated ability to impact the business quickly and have an effective combination of tactical and strategic skills. Success in dealing in a global, matrixed organization structure will be necessary for the successful candidate. Must have demonstrated expertise leading a complex global supply chain organization and ability to provide both technical and managerial leadership to his/her organization –
• Good communicator and team player
• Demonstrate interpersonal and leadership skills
• Ability to work well with people at all levels
• Fluency in English communication and written skills