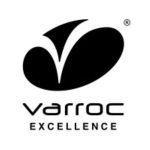
Varroc
About Us
Founded in 1988, Varroc group is a global tier-1 automotive component manufacturer and supplier of exterior lighting systems, plastic and polymer components, electricals-electronics components, and precision metallic components to passenger car, commercial vehicle, two-wheeler, three-wheeler and off highway vehicle (‘OHV’) OEMs directly worldwide.With 36 world-class manufacturing facilities and 16 R&D centers in 10 countries, Varroc group is on an exponential growth trajectory clocking a sale of 1.5 billion USD in 2016-17. The company is one of the leading global passenger car lighting suppliers and amongst the top 2-wheeler automotive component supplier in India. Varroc offers best design solutions that give customers a competitive edge in their markets.
Job Requirement
PRINCIPAL ACCOUNTABILITIES
(Accountabilities associated with the job)
Quality Control & Improvement:
▪ Conduct RCA of recurring issues (internal/external customer), analyze & implement timely CAPA for fixing gaps to ensure no repeated issues.
▪ Ensure action plans from audits are implemented to close all the non-conformities.
▪ Ensure all laid out procedures and tests and QMS documentation are implemented as per VQS.
▪ Develop the Incoming Quality check plan with respect to sampling plan and at par with Customer specific requirements (for Raw materials, BOP etc.)
▪ Conduct rating process for suppliers on quality parameters & functional/fitment checking of parts to be dispatched.
▪ Ensure parts to be dispatched by plant are checked for rust, dust, dent, damage, mechanical parameters etc. and conduct final visual inspection.
▪ Prepare various reports (Audit, CAPA, Complaints etc.) independently.
▪ Analyze process to find improvements, analyse the root cause of any problem that occurred with CFT, and identify any non-value-added activities
▪ Choose statistical technique with optimum amount of data required to ensure adequate resources and due dates are met for test report writing, with supervision Quality Assurance:
▪ Communicate the importance of the implementation of QMS procedures to all units.
▪ Cascade the concerned procedures to the respective process owners (Engineering, Production, PPC,Logistics, etc.)
▪ Design, implement and document procedures for process control, process improvement, testing and inspection, with limited supervision.
▪ Define metrics for measuring performance on quality parameters in units.
▪ Develop procedures for end-to-end quality assurance from sample collection, analysis to disposal
▪ Conduct audits of manufacturing process parameters, Product & System and ensure deviations are corrected
▪ Recognize causes and consequences of quality issues that are not readily apparent while doing cause analysis.
▪ Identify gaps in information and predict/gather relevant data in order to continue analysis and/or initiate suitable corrective action
▪ Use GD8 principles / Customer Specific formats to solve issues in the plant related to Quality of process and Product.
▪ Ensure Lesson Learnt, PTDB for all the failure in-house & customer are updated timely to Design team for future reference to ensure No re-occurrence of issues.
Quality Systems Application:
▪ Understand customer quality requirements (process and product characteristics)
▪ Be active member in CFT for development of Process documents during the Product Planning process (Gate 0) and all steps of DFMEA
▪ Participate as CFT member to Calculate the SOD (Severity x Occurrence x Detection) number or risk priority number (RPN) as part of PFMEA
▪ Develop robust Control Plans ensuring effective SOPs and WI (Work Instructions) at par with PFMEA.
Quality Alignment with New Product Development:
▪ Support concurrent engineering efforts by participating in design & development projects representing quality assurance and the customer
▪ Be part of CFT with R&D, ME team to compile the DFMEA matrix taking inputs from all team members.
▪ Implement if there are no new technical inputs required In case of ECN, else coordinate with PM & TC for changes
▪ Collect PTDB (Past Trouble Database) i.e. TGW (Things gone wrong) of earlier projects and TGR and make team members aware of the same
Customer Complaint Management:
▪ Ensure process fool proofing (Poke Yoke) – Detection & Occurrence Poke Yoke
▪ List the no. of Poke Yoke installed in Plant
▪ Conduct Poke Yoke Audit at defined frequency through rabbit test (NG Sample) & Negative Validation
▪ Ensure all deviations are approved by Plant quality Head supported by Plant Head
▪ Ensure 100% On time CAPA index, Replication, plan adherence, cascading for complaints involving machine operators closure of all mplaints,submission of CAPA within stipulated time Quality Management System adherence:
▪ Communicate the importance of QMS procedures to all units, during roll out, implementation & updates
▪ Track changes in QMS implementation at plant and deal with issues if any
▪ Support the development and administration of the customer CAPA, internal non-conformance according to Varroc Quality Management System
▪ Utilize various tools to evaluate the effectiveness of the quality system including management reviews,internal audits, feedback from internal and external customers, warranty data, and traceability, etc.
▪ Monitor progress status against open issues of all audit engagements to ensure closure.
▪ Ensure retention of all customer documents as per CSR timelines
▪ Assist QMS Head in development of QMS procedures which are aligned with Customer specific requirements