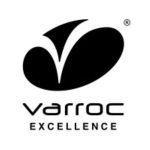
Varroc
About Us
Founded in 1988, Varroc group is a global tier-1 automotive component manufacturer and supplier of exterior lighting systems, plastic and polymer components, electricals-electronics components, and precision metallic components to passenger car, commercial vehicle, two-wheeler, three-wheeler and off highway vehicle (‘OHV’) OEMs directly worldwide.With 36 world-class manufacturing facilities and 16 R&D centers in 10 countries, Varroc group is on an exponential growth trajectory clocking a sale of 1.5 billion USD in 2016-17. The company is one of the leading global passenger car lighting suppliers and amongst the top 2-wheeler automotive component supplier in India. Varroc offers best design solutions that give customers a competitive edge in their markets.
Job Description
Production Planning
▪ Understand the targets set for sales, variable cost, fixed cost, etc. set for Business Development
▪ Draw own functional priorities and participate in the cross functional team to convert these targets to relevant
targets for production; Propose PPM targets, PQCD cost, etc. at the beginning of year to ensure EBITDA objectives
are met
▪ Develop plans to ensure minimum production cost in line with the business plan to achieve the PQCD targets by
ensuring continuous improvement.
▪ Conduct discussions with the key customer – Purchase, to finalize material planning for the coming month, identify and provide suggestions for resolution of issues
▪ Execute the production plan as per the PPC guidelines to meet the Customer schedule.
Improvement Projects
▪ Define projects in line with the overall improvement targets for production, maintenance, etc.;
▪ Provide inputs to ME team on project planning and execution; Analyze and identify lines with opportunities to
improve/ reduce cycle time, etc. Provide ideas and brainstorm with the improvement ME team on opportunities
and scope for improvements in manufacturing processes through process elimination, process merging, changes in
layout etc.
▪ Raise monthly capex requirements for projects, share input on manpower savings with HR and other factors
impacting PnL (fixed/variable cost) for review by Plant Head
Cost Reduction
▪ Improving life & identifying alternate to reduce consumable cost by identifying and implementing Kaizens.
▪ Cycle time reduction of bottlenecks by changing program, modifying machine assembly & manpower training etc.
▪ Improve productivity by multi machining, reducing cycle time & training to new machine operators on Machine
Operations, Job Handling, Product quality specification.
▪ Monitoring Kaizen, 5s & TPM training & train employees for multi machining & multi skilling.
4. IHR & Customer Complaints
▪ Monitor & Reduce IHR level by analyzing the product and process defects and taking corrective action by improving
production process and deploying the same horizontally.
▪ Review day to day production process for rejection monitoring (process wise & product wise) to identify top defect
for down the line Implementation of corrective and preventive actions.
▪ Monitoring SPC (Statistical Process Chart) & PQC (Process Quality Chart) repots to correct production process.
Safety
▪ Monitoring implementation of EHS guidelines, implementing various EHS systems, monitoring strict usage of PPE’s.
▪ Monitoring, implementation & adherence to health and safety procedures & documenting near miss, may happen& unsafe condition to take necessary actions to prevent accidents.
▪ Keeping the records of near miss accident & implement near miss kaizens to ensure zero accident & build safety
culture.
▪ Monitoring for audit compliance & taking corrective actions to clear nonconformities.
Internal Audit and Documentation
▪ Monitor internal audit for auditing adherence to Safety, TPM,5s
▪ Ensure completeness of documents for IATF, Customer & other external audits
▪ Workout and implement SOP’s (Standard operating procedures), OPL (One Point lesson) for production process.
▪ Monitoring Employees Skill matrix & Preparing Production MIS.
▪ Document preparation for IATF, OSHAS, Customer & other external audits.
Review and execution
▪ Coordinate and seek alignment across functions/ departments such as maintenance, purchase, store, HR, etc. to
achieve the set targets
▪ Anticipate and resolve escalated issues, remove roadblocks synergies and ensure overall targets are achieved
▪ Analyze, consolidate and put up manpower requirements to the HR department
▪ Closely monitor early failure report (IFR), inhouse rejection cost (IHR), scrap cost to achieve set targets
Stakeholder management
▪ Manage stakeholders such as maintenance, quality and improvement to achieve common objectives e.g. with
maintenance to ensure maximum uptime of machines
▪ Engage with maintenance and improvement department on the lines to be run 24*6, maximize uptime,
improvements with minimal cost, etc.
▪ Work with quality team on smooth customer audits, monitor house rejection against set targets and reduce
rejection trends, maintain customer PPM, etc.
Team development
▪ Participate in recruitment process to identify the right talent across positions within the team
▪ Establish individual performance expectations and regularly review individual performance of the team
▪ Identify and create development opportunities for team members to enhance functional knowledge
▪ Plan for second line development and scale up, provide additional responsibilities for team from time to time.